Remote Problem Solving for Reliable Solutions
/For Randy Estep, the bottom line is designing a safe, cost effective and reliable solution for the application—getting the right pump with the right seal to move a specific fluid for a specific reason. And with a company as large as Dow Chemical, there is an almost endless range of possibilities. Randy works globally from his West Virginia home as the Mechanical Technical Associate, Hardware Discipline Technology Center, and must use his depth of knowledge, experience, and communication with process engineers, maintenance engineers and production representatives to visualize the circumstance and design the best solution.
By Michelle Segrest, Navigate Content - Reporting for Pump Engineer
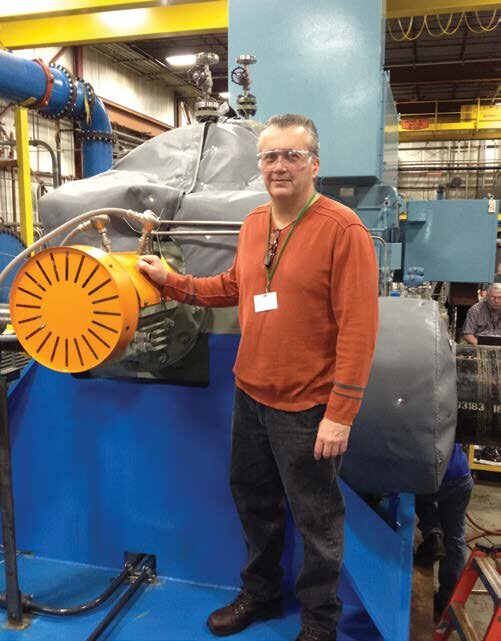
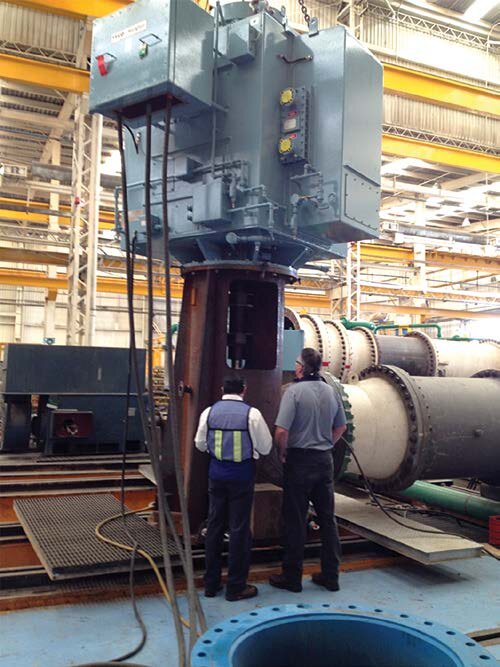
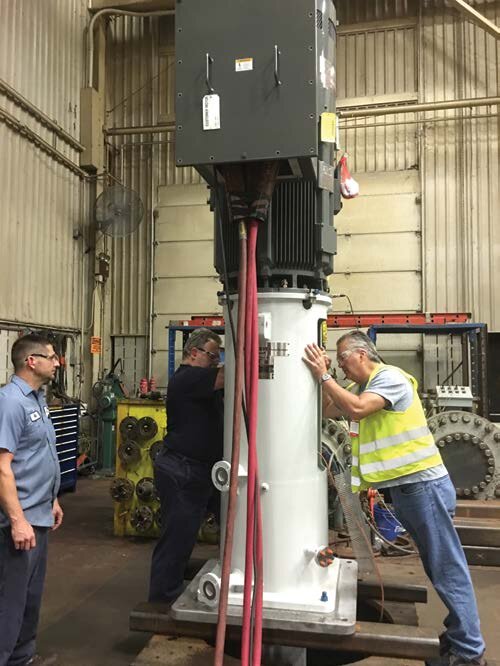
Randy Estep’s experience is deep and diverse. For nearly four decades he has done everything from designing, installing, maintaining and troubleshooting equipment to ordering parts, analyzing bids and working directly with manufacturers and suppliers. This depth of experience prepared him to troubleshoot and make process and equipment improvements every day for Dow Chemical.
“To be an expert, in my opinion, you need a wide range of experience combining both field support and project support,” he says. “Understanding the engineering fundamentals is very important. The value I bring to capital projects and designing new equipment is because I have experience on both sides of the fence.”
He graduated with a Bachelor of Science in Mechanical Engineering from West Virginia Institute of Technology in 1981. His first working experience was with Union Carbide Corporation in its Machinery Engineering department, where he was primarily involved with engineering and procurement support for pumps and mechanical seals for major capital projects. He also provided support to a local Union Carbide plant engineering department in Institute, West Virginia. He then moved to a large chemical complex run by Rhone Poulenc where he spent about a decade working in a plant maintenance technical services department as a reliability engineer and then group leader.
Thereafter, he joined Dow Chemical in 2001, where he has been ever since. As a Mechanical Technical Associate for Dow Chemical, Randy is the Global Pump and Seal Technical Solutions Team Leader with roles that include the development and maintenance of the Dow Most Effective Technology (MET) program for pumps and mechanical seals.
Pump Supplier Management Action Team
This program is an internal specification file with procurement guidelines, safety requirements and minimum design criteria. He provides subject matter expertise for pumps and mechanical seals to process design, reliability teams, production units and capital projects. Randy also serves as part of the Pump Supplier Management Action Team, for which he is responsible for maintaining the pump approved suppliers list, monitoring supplier performance and performing supplier quality audits.
“I am the technical arm of the team,” he says, and he works closely with his purchasing counterparts. In addition, he is Vice-Chair of the ASME B73 Committee for Chemical Standard Pumps and has participated on several API 610 and 682 Task Forces.
His biggest role is providing design guidance and consulting to capital projects and production units and to proactively identify innovative technologies or maintenance solutions to make the plants run safer and more reliably.
He is part of a larger Dow global Mechanical Discipline Team that covers multiple equipment types, but Randy leads the team of pump and seal technical subject matter experts.
His role covers a broad range that starts with design. For example, processing engineering may have a problem where they need to move a fluid from Point A to Point B, and they may not know the best pump and seal technology needed to do that reliably.
“In this case they come to me and I’ll work with them to apply the best pump design technology for that service,” he explains. “I make recommendations on the right equipment for a specific application. If there is problem equipment in the field—for example, a bad actor pump that fails—and they want to design improvements, they will come to me to help them understand why it’s not functioning as it should and what they can do to make it better.”
After making the recommendations, Randy then supports the capital project in reviewing bids, witnessing tests and helping construction to install the equipment correctly. He designs the pump and the seal to support the process need. There may be reports where operators are tearing up the equipment, but the process demands that the operator do what he’s doing. In some cases, the equipment wasn’t designed correctly to meet the process demand in the first place.
Randy explains: “For example, if you have a batch operation that requires emptying the tank, there may be a bad actor pump because the pump keeps running dry. We may blame the operator, but the operator was just doing his job. We need to design the equipment to account for that process demand rather than blaming the operator.”
As a problem solver providing global support for all of Dow Chemical, Randy could be working with facilities in Saudi Arabia, Thailand, Canada, Texas, Kentucky, California, or anywhere in the world where Dow has process units. Just as he is not limited by geography, his product range is not limited to certain products—it could be anything Dow makes.
Maintenance & Engineering Best Practices
Randy enjoys combining his maintenance and engineering experience to help others solve problems. His experience is primarily with centrifugal pumps, but just about any type of pump one can think of has come across his desk over the years. The most common construction standards have been ASME B73.1 and API – 610.
“My maintenance reliability role was in a large complex that included pesticide manufacturing,” he says. “Some of the products that went through the pumps were highly hazardous, dirty and corrosive. We struggled to increase reliability and reduce maintenance cost in a business environment that only supported a small group of engineering resources to tackle those tough reliability issues.”
Randy’s team was able to pull together a successful Pump Bad Actor Reliability program that focused on increasing overall pump reliability by targeting installations with a high incidence of repair.
“Typically, a very small percentage of installed pumps accounts for a disproportionately high percentage of a plant’s total pump repairs, and our plant was no exception,” states Randy. “By setting up tracking systems and identifying these pumps, we were able to focus our limited resources on the high-value maintenance issues which resulted in a significant positive impact to the plant’s total maintenance costs.”
The program included root cause failure analysis to design permanent solutions for recurring problems, addressed maintenance repair practices, repair records and spare parts. It also engaged operations with smart equipment inspections and operator training.
For new installations, a process engineer will build a data sheet and then work with Randy to define the full operating spectrum to determine the best pump type, seal, auxiliary systems and any process modifications to ensure a cost effective, reliable and safe design is specified. With environmental and safety regulations getting tighter and tighter, this becomes a challenge.
Industry Trends & Advanced Technology
With almost four decades of experience, Randy says he remembers a time when he would place a penny or a screw driver to feel or listen to equipment to see if it was vibrating or behaving in a way that required maintenance or improvement.
With the onset of instrumentation, predictive maintenance tools and monitoring equipment, times have changed.
He believes the rapid development and availability of affordable wireless equipment monitoring systems has a lot of potential (especially for bad actor pumps and rotating equipment) as an investigative tool for better understanding of operational impact on reliability. All of Dow Chemical’s major sites have predictive maintenance groups that perform periodic monitoring. There is also continuous monitoring for things like vibration for the larger equipment.
Dow has recently piloted the use of devices that are Bluetooth enabled that can be attached to small equipment to troubleshoot or to better understand problematic issues.
“If you have these devices tracking trends, it can tell us a lot,” says Randy. “These devices are inexpensive and can be attached to the equipment temporarily or permanently. They capture data with regard to vibration and temperature and are a valuable asset, especially in bad actor programs where you are targeting equipment that has poor reliability. You can gather data that helps you design improvements.”
Challenges With Aging Workforce & Aging Facilities
Randy says he can remember being a young engineer and admiring the more experienced engineers who mentored him.
“When you first start out as a young engineer you work with older guys, like I am now,” he states. “You always wonder how they know so much. I understand now that it is through time and experience that you learn…and then you become one of those old guys.”
He acknowledges that the talent gap is an industry issue that is not going away. It is a real problem and the industry in general has been slow to react. However, Randy has been very encouraged lately because there are a number of smart and motivated young engineers in the pipeline showing interest in pursuing a technical career path.
“The tide may have finally turned in a positive direction,” he says. “Companies are more and more supportive about providing developmental opportunities and recognizing the value technical expertise brings to the bottom line.”
As plants age, the problem with replacing obsolete parts is growing. Randy continues to encounter this issue. The plant where he first started working had equipment that had been in service since the 1940s, he explains. Learning to deal with obsolete and aging equipment was a way of life, but he has helped with pump replacement projects over the years.
However, as he explains, these projects were probably driven more by environmental and safety concerns than the age of the equipment.
A father to two daughters and grandfather to 3-yearold and 8-month-old boys, Randy has solid advice for those entering the industry:
“Attending networking events such as Pump Summit Americas 2018, where the pump industry’s finest experts gather to share knowledge, ideas and experiences, is critical to the career development of those new to the industry as well as the most experienced. I have benefited immensely by attending these types of events over the years and highly recommend anyone involved with pumps to attend all or as much of the conference and exhibition as possible”.
He adds that through the years there have been a lot of equipment, maintenance and technical experts that have quietly made the equipment better and found ways to run the equipment more reliably, but they kept quiet and never told anyone. When business times are hard, their value may not be realized. “My advice is to make sure that if you do something good and save the company money or help a plant improve in some way, let your voice be heard.”
Michelle Segrest is President of Navigate Content, Inc., a full-service content creation firm. She has been a journalist for more than three decades and specializes in covering the people and processes that make a difference in the industrial processing industries. Contact her at michelle@navigatecontent.com