Why Pumps Fail - Avoid Common Specification Mistakes
/When it comes to keeping food and beverage pumps running efficiently, a pump expert identifies some common specification errors you should avoid.
By Michelle Segrest, Navigate Content, Inc. - Reporting for Efficient Plant Magazine
For the past 33 years, Jim McCormick has been solving problems for his sanitary and process equipment customers. Most of the time, he says, these problems could have been avoided.
“There are a lot of things I’ve learned over the years as far as things that can go wrong and why pumps fail,” said McCormick, director of sales and corporate development applications and technical sales engineer for SANI-PUMP Inc., Sanitary Pumps and Equipment of Chattanooga, TN. “I’ve made a list of some of the reasons this happens. I work closely with my customers to hopefully avoid these common mistakes.”
Misapplied pumps (specify correctly)
Misapplied pump selection could be the fault of the pump salesman or the person responsible for specifying it, McCormick said. “Sometimes, it’s a combination of both. I run into this a lot—customers have a good pump but maybe the seals have been leaking or the pump is cavitating. By process of elimination, most troubles can be corrected.”
Every application is different. There are several factors to consider when specifying a pump for a particular application. Many companies use tools that are designed assist in sizing and recommending the correct pump for specific needs. These include pump-sizing programs, calculations, and conversion software. “Experience and knowledge are often the best tools available,” McCormick noted.
The first task in sizing the proper pump is to obtain as much information about the application as possible, he explained, including flow rate, discharge and suction pressures, fluid information, temperature, seal type, viscosity, specific gravity, and power requirements.
Pump assembly error (always read instructions)
McCormick said that, even though most pumps and seal kits come with detailed installation and assembly instructions, improper assembly is a common mistake with sanitary equipment.
“I don’t know if it’s that guy thing where guys just don’t bother reading instructions,” he said. “And sometimes the operator or mechanic is very experienced and knows what to do, but because he doesn’t read the instructions, there is one small detail that gets overlooked. And small details can make a big difference.”
McCormick explained that it could be a detail such as loosening the set screws on the drive collar and repositioning it. Often, the assembly mistakes can be made at the manufacturing point.
Improper assembly can also adversely affect the testing results. “Any time there is a rotary seal or mechanical seal, there is room for error in assembly,” he said. “A mechanical seal can sit on a spring, and the pressure from that spring is what pushes the rotating element up against the stationary element. The stationary element could be a back plate made of stainless steel or it could be another embedded silicon carbide or tungsten carbide, or ceramic. All of these details make a difference in how it is assembled.”
Inaccurate or insufficient information (there can never be too much information)
Not enough information—or the wrong information—can mean certain failure, McCormick stated. “Sometimes I’m asked why is it important to know the temperature,” he explained. “If the temperature is too high, this can cause certain seals to fail. I insist on knowing the temperature. I’ve had calls from people saying they were pumping beer at 212 degrees and they can’t understand why the seal is cracking. Well, if I had known that temperature before I sold them the pump, I would have known not to use that particular seal.”
Knowing the required horsepower and speed of rotation is also essential. “For example, you cannot pump yogurt or ice cream or milk or beer at high speeds because it will create foam or damage the product integrity,” McCormick explained. “In many cases, you need two speeds—one speed to pump the product and another for CIP (clean in place) operations. You can’t pump beer at 3,600 rpm because it will compromise the end product. All of those little things have to be taken into consideration, and that’s why we ask so many questions.”
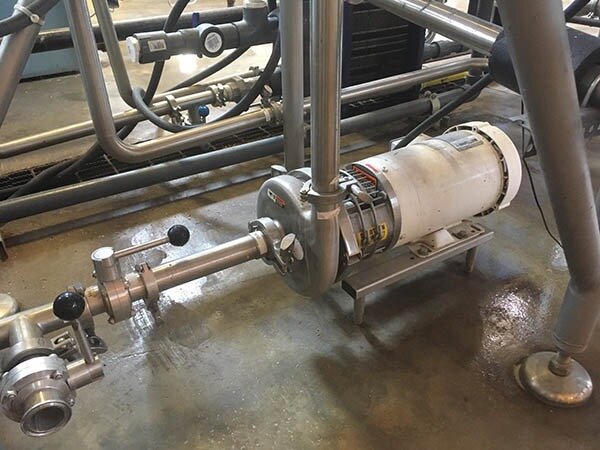
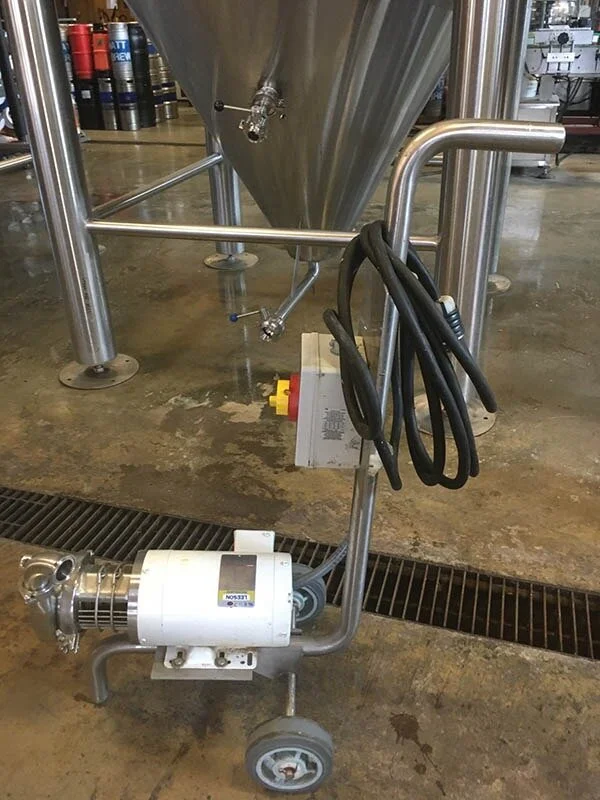
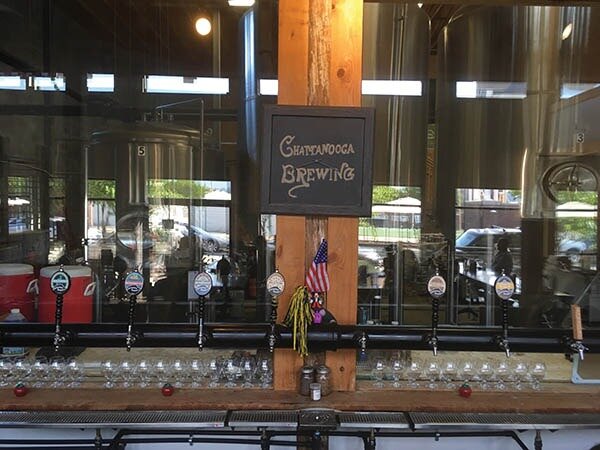
Operator error (follow procedures)
McCormick said 75% to 80% of his troubleshooting work involves centrifugal pumps. The rest of the time he spends working on rotary-lobe, positive-displacement, and gear pumps, with the occasional seal-less pump.
An example of operator error with these pumps is letting a non-self-priming pump run dry. Seals will fail quickly without proper lubrication. “It’s the product that lubricates the seal—whether it’s beer or water or milk—the liquid is what is going to lubricate the seal base, which is the stationary and the rotary element. If the operator doesn’t realize this, he may not flood the suction head of that pump which could cause it to burn up the seal.
Eventually, it’s going to cavitate and make so much noise they are going to want to leave the room. I’ve had people call me and say the cavitation sound has scared them so much they didn’t want to go near it. This only happens occasionally. Most operators are pretty savvy. But it’s important to be aware.”
Misapplied seals (specify correctly)
You cannot only misapply an entire pump, but you can also misapply an entire seal, McCormick said.
“I do a lot of work in breweries, and the people who brew beer want it as hot as they can get it,” he said. “They want to brew at 210 to 212 degrees—sometimes hotter than that. The problem with temperatures like that is they generally use a ceramic seal, but ceramic does not handle thermal shock very well. Thermal shock is like the screen door at your house. When it is hot it expands and it sticks sometimes. When it’s colder, it opens and closes freely.”
Almost every material known to mankind expands when exposed to heat, McCormick said. “In the case of ceramic, it inherently does not expand. It wants to, but it can’t. What I mean by ‘it wants to, it tries to, and it can’t’ is that it develops microscopic hairline cracks and eventually those turn into larger cracks, and the seal will begin to leak.
“Beyond that, there have even been some instances where a ceramic seal totally disintegrated or blew apart—not into a million pieces, but the cracks can become so many and so big that everything just falls apart. So, for high-temperature applications, I get people to shy away from ceramic and instead use silicon carbide or tungsten carbide because they are much more resilient to thermal shock.”
Contamination (don’t lose the batch)
With rubber seals and parts, contamination can be a problem. Unwanted elements can get into the product being processed if the seal is leaking.
“It’s not just messy when a seal leaks,” McCormick said. “It can also affect the material. Some of that can be removed during the filtration process. A lot of breweries have some type of filtration at the end of the system before it goes to packaging or bottling.
“Some plants don’t do it like that. Some think that cloudy beer is the death of beer. I saw a bumper sticker once that read, ‘If God wanted our beer to be filtered, he wouldn’t have given us livers.”
This contamination can be a concern, especially when processing sanitary products. “We have all heard about product recalls where there may be metal shavings in a product that may turn out to be parts of a seal,” McCormick said. “This doesn’t happen often because usually when the seal starts leaking they shut the system down. But that doesn’t mean that something can’t get in there, and that is when your quality-control people get involved with the product.
“There is always some type of inspection going on. Every process has a sample batch. They will draw from each one. If there is any type of contamination they will do a full inspection and sometimes they will have to trash the entire batch.”
Lack of proper maintenance (focus on failure prevention)
A best practice for most companies is to have regularly scheduled maintenance written into their procedures. In many cases, this happens during changeovers. Many elements are inspected, including seals, gaskets, and O-rings. If they are compromised in any way, they are replaced.
“Proper maintenance is going to save you money in the long run,” McCormick said. “Downtime is a huge expense. If you don’t change that seal in a reasonable amount of time, you are just waiting for the seal to break and chip. They can chip for a lot of reasons. Cavitation can occur and you might get parts of seal in your process. Now you will have to dump your entire batch. That’s expensive.”
If you follow your own protocols and procedures, this can be avoided, he said. “I recommend a focus on failure prevention before failure analysis,” he said. “Whenever there is a failure they usually write up a failure analysis. They do this to find out why the failure happened.
“If you set your sites on a higher level and go for failure prevention you’re going to have less failure analysis to do. Prevention before failure—this is very important. People are finally starting to figure that out.”
Insufficient replacement parts (don’t be a pirate)
When replacement parts that were not designed/manufactured by the original-equipment manufacturer [OEM] are used, pump failure can happen, McCormick stated.
“In some cases, it’s okay to use ‘pirate’ parts, but only if the manufacturer uses FDA-approved materials like rubber compounds and seal materials,” he explained.
“There are a few who ruin it for the others because they get cheap and don’t go through the correct process. But remember that putting someone else’s parts into an OEM component voids the warranty. This kind of goes hand in hand with preventive maintenance. Cheap is not always better.”
McCormick advises asking the manufacturer or supplier of pirate parts to send you the documentation of 3A or FDA approval to confirm that the compound that was used is made to FDA regulations.
Not using proper CIP procedures (keep changeovers clean)
Clean-in-place [CIP] procedures are critical in food and beverage processing (see “Top Reliability Tips for Maintaining Food & Beverage Pumps,” Maintenance Technology, October 2016). The pumps used in food-and-beverage processing applications can also be used for CIP procedures as long as proper procedures are followed.
“That pump is used for multiple applications,” McCormick said. “At a typical dairy, some [pumps handle products such as] bottled water and milk, skim milk, buttermilk, 1% milk, and 2% milk. Some even run through an orange drink…a lot of that is produced in dairies. As long as it has been cleaned in place and verified cleaned in place and then tested, it is okay.”
When various colors or flavors are processed, different pumps may be used. Again, however, details such as temperature and pressure, and seal selection, must be carefully considered.
“Consistency is important when processing any beverage or anything edible,” McCormick said. “Every bottle or can of soda needs to look and taste the same as the last 5,000 bottles or cans. Avoiding all these common mistakes can help to keep sanitary equipment running efficiently and reliably.”
Mechanical Seal Faces
Mechanical seal choices have become increasingly popular in the pump industry, according to Jim McCormick, SANI-PUMP Inc., Chattanooga, TN. Many companies develop a set of pump-seal specifications to make it easier for their customers to select one or more seals for an application. The lack of a company specification can cause problems with seal inventory, installation, and interchangeability. Many plants are accepting seal components with unidentified and/or inferior materials, making troubleshooting a nearly impossible task.
According to the American Seal and Packing Co. (americansealandpacking.com, Santa Ana, CA), a good company specification for pump seals will include the following:
• seal materials with the widest range of chemical compatibility
• seals that are easy to install
• seals that operate over a wide range of temperature, pressure, and speed
• features that make seal repair easy and low cost
• seals that require the least amount of inventory and spare parts
• designs that allow the easiest conversion of packed pumps to pump seals.
The most common seal-face materials:
• Carbon or carbon graphite. This is the old standby, McCormick said. Carbon, or carbon graphite, seals offer the greatest economy and lubricity for sealing non-abrasive products. This is good for clean, abrasive-free materials. It self-lubricates to reduce heat and extend service life and works great with all other seal materials.
• Ceramic. Generally, a 99.5% aluminum oxide offers excellent wear characteristics due to its hardness. It is chemically inert and can be applied to nearly any product. In the sanitary environment, ceramic offers the best resistance to sticky liquids, such as syrups. Ceramic cannot handle thermal shocks. It has zero tolerance for thermal expansion and easily cracks or shatters. Like most other materials, it wants to expand with heat, but it cannot. Ceramic is much more resistant to abrasive materials than carbon. It is also corrosion resistant and inexpensive. Ceramic material is most commonly paired with carbon.
• Silicon carbide. This is a bluish-black material created by fusing silica and coke. It is in the same family as ceramic (due to the silica), but has much better lubrication qualities and is harder. It contains no silicon that can leach into the process and is excellent in an oxidizing environment. Silicon carbide has good thermal-shock resistance due to its low thermal-expansion coefficient and high thermal conductivity.
“In summary, silicon carbide’s combination of hardness, strength, and temperature resistance gives it excellent capabilities for services in a wide range of applications where high speeds, high pressures, and chemical and abrasion resistance are required,” McCormick said.
Michelle Segrest is president of Navigate Content Inc., and has been a professional journalist for three decades. She specializes in creating content for the industrial processing industries. Contact her at michelle@navigatecontent.com.
RELATED ARTICLES
The Cost of Clean Water - How Pumps Play a Role in the Water-Energy Nexus
Isolate the Problem to Solve the Problem
How to Build a World-Class Manufacturing Facility
Deep Tunnel Super Pumps Pushed to the Edge in London’s Lee Tunnel
This page contains affiliate links. If you click on the product links and make a purchase, it allows me to make a small commission at no extra cost to you! Thank you for your support and I hope you find value in this content!